Rail
Growing Use of Composite Materials in The Rail Industry
Rail sector OEMs and tier 1 & 2 product suppliers are increasingly switching away from more traditional metallic (and asbestos) based engineering materials in favour of alternative, more sustainable, fibre-reinforced (FRP) thermoset resin-based materials. Rail Composites are providing significant life cycle benefits for train operators to meet carbon-neutral environmental objectives. Composite materials in the rail industry are also helping to lower operating and maintenance costs.
High-performance, fire, smoke and toxic fume (FST) rated, lightweight FRP composite materials in the rail industry are increasingly being specified to refurbish in-service rolling stock and on next-generation trains, which need to have greater operating efficiencies, better performance, less energy consumption and lower emissions.
Rail
Permaglass® rail composite solutions
For more than 50 years, Permali has been an approved OEM supplier of high-performance FRP composite materials in the rail industry, especially within the UK rail sector.
Permaglass® solid laminate sheet and cored sandwich panel products are specified for demanding safety-critical applications on locomotives and rolling stock for both underground and overground passenger and freight trains. Depending on the application, Permaglass® products and rail composites are formulated to meet critical rolling stock regulatory standards including RSE/STD/013 & /014 and BS EN 45545-2:2013 for fire, smoke and toxic fumes (FST).
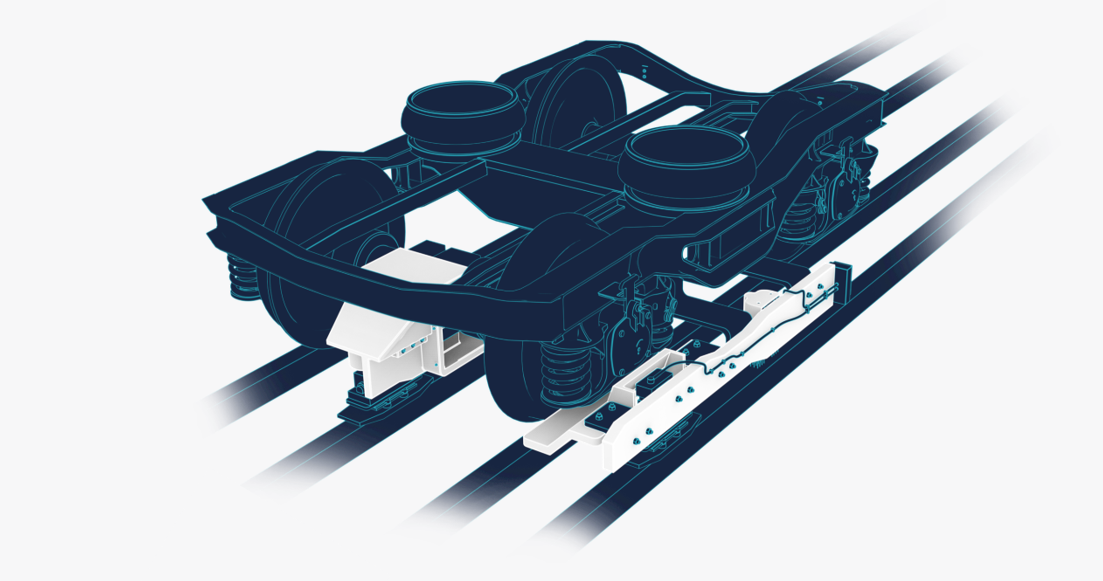
Rail
Permaglass® composite sandwich panels
Permali has developed rail composites which are lightweight, high strength, energy absorbing, composite sandwich design flat panels up to 50mm thick, moulded with Permaglass® FRP laminate outer skins. Permaglass® composite sandwich panels are used for fabricating components that can improve the crashworthiness of locomotive cabs and reduce weight. Permaglass® electrical insulation composite laminate sheet grades have also been developed which comply with RSE/STD/013.
Permaglass® FRP sheet composite materials in the rail industry are supplied as semi-finished stock materials in sheet thicknesses from 0.3mm to 60mm, which can be cut to size as required for customer production needs. Permali also has 3 & 5-axis CNC machining, bonding, coating, painting and assembly capabilities. This enables finished, ready-to-install sub-assembled rail composite components with metal fixtures to be supplied to rail customer designs and specifications.
Key Features and Benefits:
Design options
High strength
Meets standards
Halogen free
Outstanding resistance
Alternative materials
Rail Applications
Permaglass® MER20 & MER35
Rail composites such as Permaglass MER20 & MER35 sheet grades offer halogen-free, fire-retardant electrical insulation and resistance against arcing and tracking, combined with excellent mechanical properties and easy machinability. Both grades meet stringent safety regulations specified by London Underground including B2 476 Parts 6 & 7; BS 6853 App A & B; UL94V0; RSE/STD/013 and RSE/STD/014 Part 1 Issue A Fire and Arc Protection Standard. Making them perfect composite materials in the rail industry.
MER Components fabricated from rail composites such as MER20 and MER35 include: shoe beams and arc boxes/barriers for electrically powered units, and provide an excellent alternative to asbestos-based materials.
Permaglass 22FE materials are a range of standard fine weave glass epoxy laminates which can be precision CNC machined to produce high strength electrical insulation components with high temperature performance and electrical insulative properties. Permali is able to manufacture sheet sizes up to 4.8×1.9m.
Permaglass MFM is a rail composite, fire-rated pressed glass fibre reinforced (GRP) phenolic sheet laminate with a decorative melamine paper layer included on the visible surface. MFM laminates are specified in train interiors as the protective top layer for wall, door and ceiling panels where a high degree of scratch and graffiti resistance is required.
Semi-finished sheets, typically in standard 2.44m x 1.22m sizes from 0.3mm thick are supplied to fabricators of interior decorative panelling for rolling stock. Permaglass MFM is currently in use on London Underground tube trains and nationally on overground passenger train carriages. These are very popular composite materials in the rail industry.
Rail
Bespoke Solutions for Rail
Permali is also able to develop bespoke composite solutions for rail customers.
The R&D, design and process engineering teams understand how to deliver the advantages of rail composites. In-house technical expertise in resin formulating, reinforcements, cores and processing is used to develop customised high-performance, halogen-free composite materials to meet stringent regulatory rail standards related to: crash impact, electrical insulation, ignition, flammability, surface spread of flame, and toxic gas emissions.
See our products in action
Case Studies
Following the fire disaster at King’s Cross St Pancras tube station in 1987, stringent new fire safety regulations were issued for the governance of materials used on the London Underground. To this day these fire safety regulations, formerly BS6853, and now incorporated in the European railway standard for fire safety EN45545, include some of the most demanding requirements in the world for composite materials in terms of flammability, smoke and toxic fume emissions. These regulations are applicable to all composite materials in the rail industry.
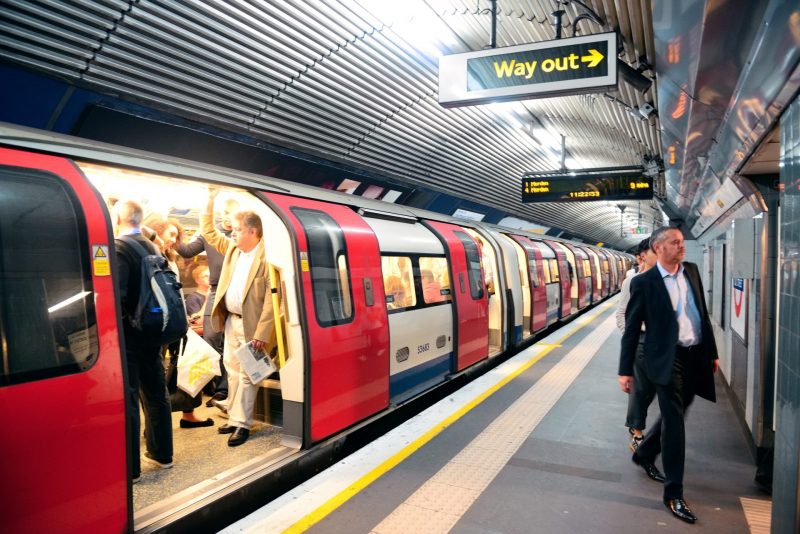