Composites for Aerospace
Aerospace
Advanced Aerospace Composite Solutions
Permali has been a leading provider of aerospace composite solutions for over 50 years. The company specialises in Permaglass® advanced composite materials, aerospace composites, and precision-machined components for both civil and military aircraft, including fixed wing planes and helicopters. Permali holds AS9100 certification, underscoring its commitment to aerospace quality standards.
Additionally, Permali produces a wide range of Tuftane® thermoplastic polyurethane (TPU) elastomeric films through blown film extrusion. These high-performance Tuftane® film grades are essential for creating flexible barrier fabrics and textiles that comply with rigorous FAA aviation safety standards, suitable for aircraft and aerostats.

Permali approved supplier of Airbus
“Permali provides customer responsiveness and cooperation, well documented processes, and best practice.”
Permali are proud to announce that as of the 9th October 2023– we are officially an approved supplier of Airbus. Permali have demonstrated compliance with Airbus instructions in a repeatable, reproducible and stable way of working – and we have been granted qualification on the test Method ISO178.
Aerospace Composites & TPU Film Applications
Permaglass® composite sheet materials and Tuftane® TPU films are specified by leading aerospace OEMs, aerospace composites companies and supply chain manufacturers all around the world, who trust Permali’s proven safety and protection solutions for the following applications:
For civil aircraft, Permali aircraft composites include FAR/CS 25 fire rated grades of Permaglass FRP composite sheet materials are used for passive cargo compartment fire protection bay liners, approved by Boeing, Fokker, Saab and BAE Systems. Cargo bay liners also need to provide a tough, hardwearing internal layer that can handle baggage and cargo handling containers. Permali also supplies fire resistant anti-ballistic armour plate protection for cockpit doors on commercial passenger aircraft.
Fire resistant, low smoke and fume Tuftane TPU film grades are used in aircraft interior floors and cabin furnishing materials, providing textiles and aerospace composite laminates materials with high durability, comfort and fire safety.
Hydrolysis resistant Tuftane TPU films pigmented in bright safety colours are used in vital inflatable emergency safety equipment for passenger and flight crew: life jackets, life rafts and emergency door escape chutes. For aircraft emergency buoyancy aid equipment, Tuftane TPU film grades are formulated with additives to not only provide high elasticity, tear strength and puncture resistance, but to also be resistant to fungi and microbials. Equipment manufacturers are able to use RF welding techniques with Tuftane film to fabricate inflatables and products with high weld strength to meet required aviation safety standards.
Unpowered semi-rigid, inflatable cable tethered aerostats, such as advertising blimps, barrage and weather balloons depend on an inert gas, such as hydrogen or helium, to provide the ‘lift’ and then remain suspended in the air. High elastic strength Tuftane TPU film grades are used in aerostats for the gas-filled fabric membrane, enabling it to remain inflated for prolonged periods of time. The Tuftane film also provides the elasticity to cope with extreme changes in temperatures and pressures between the ground and at operational altitudes.
Aircraft Composite Solutions
Permaglass® FRP sheet materials are supplied as semi-finished stock materials in aircraft approved fire rated cargo bay lining and ballistic grades, which can be cut to size if required.
Permali also has 3 & 5 axis CNC machining, bonding, coating, painting and assembly capabilities. This enables Permali to also supply ready to install bespoke fabricated, finished composite aerospace components, including any metal fixtures, to an aerospace customer’s design and specifications.
The main applications where our aerospace composite materials are specified for civil aircraft include:
The key functions of a cargo bay liner is to prevent the spread of fire, smoke and toxic fumes (FST) from the cargo compartment and provide a durable internal lining. Cargo bay liners in passenger aircraft in particular need to be tough and very hardwearing, able to withstand repeated loose baggage impacts and wear from containers, boxes and pallets.
Permali supplies fire resistant (FR) aircraft cargo bay liners, manufactured using woven ‘E’ or ‘S’ glass fabrics with either an FR epoxy resin or FST rated phenolic resin grade. All Permaglass GRP composite sheet products used for cargo bay liner meet FAR/CS 25 flammability requirements and have approvals from Boeing, Fokker, Saab and BAE Systems approved.
For cost effective maintenance and repair of an operational aircraft, Permali supplies “peel and stick” patch product to repair damaged liners in situ. Cargo lining panels, particularly in passenger aircraft with loose baggage are prone to minor damage in small areas. The “peel and stick” repair patches are very quick and easy to apply by hand, requiring no special tools.
Permali’s cargo liner repair patches have been fully tested to meet the FAR25 App.F standard, with approvals from Boeing and Airbus.
Permali has extensive expertise in anti-ballistic and blast protection composite armour, supplying the Land, Sea and Air Defence industry for over 80 years. For civil aircraft protection, fire resistant ballistic armour solutions are supplied for cockpit doors, which meet AC 25.795-2A and NIJ 0101.04 Level 3A standards. Permaglass ballistic grade stock sheet material or custom made CNC machined parts are supplied to manufacturers of civil aircraft cockpit door systems.
Key products for Aerospace:
Evacuation chutes
Emergency exit inflatable evacuation chutes
Life Rafts
Inflatable life rafts
Furnishings
Airline furnishings and flooring
Life Vests
Passenger life vests/ infant buoyancy aids
See our products in action
Case Studies
The terrible September 11 attacks on the US in 2001 permanently changed the nature of air travel for everyone, and the world is now familiar with the increased security measures at airports and on-board aircraft. These measures include making aircraft cockpit doors both intrusion resistant and bulletproof, with Permali playing a major part in the worldwide programme to upgrade existing doors in accordance with new regulations from 2002 onwards.
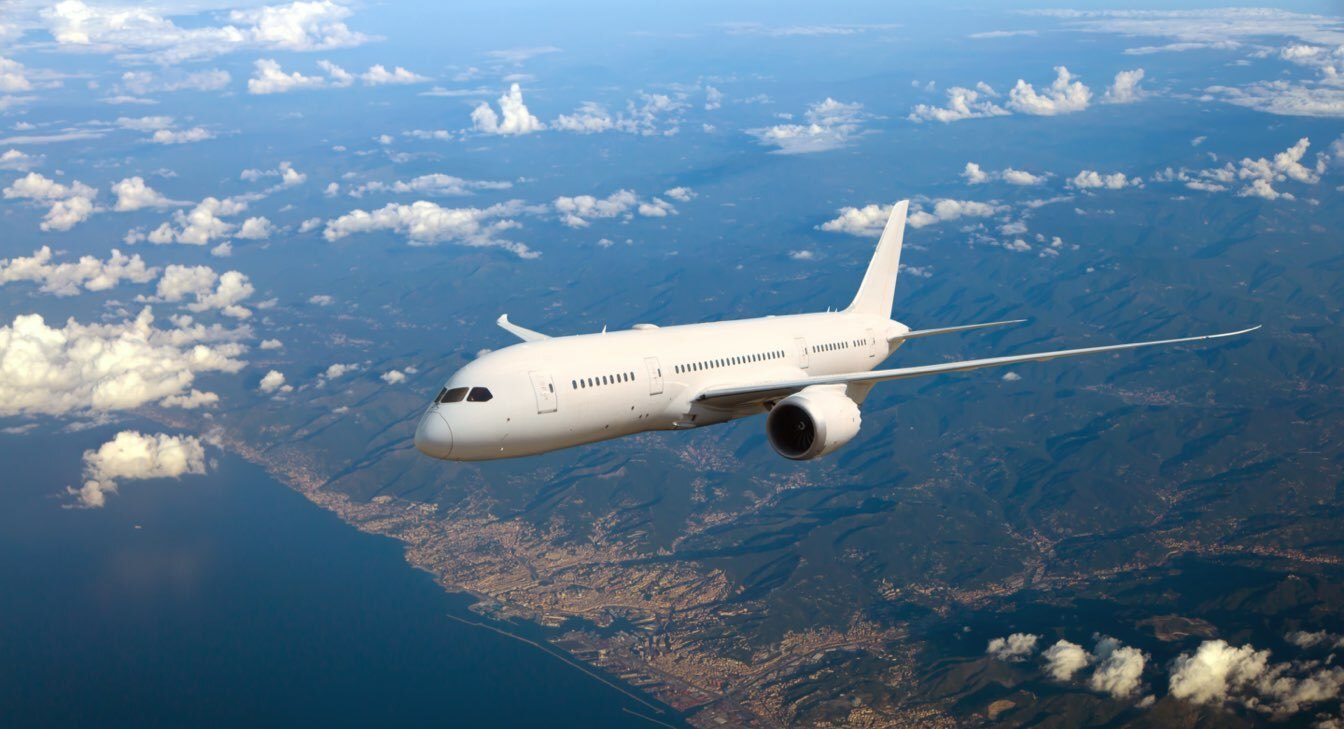