CASE STUDY: RAIL
Fire Retardant Composites for Current Collection Equipment on 3rd Rail Rolling Stock
Following the fire disaster at King’s Cross St Pancras tube station in 1987, stringent new fire safety regulations were issued for the governance of materials used on London Underground. To this day these fire safety regulations, formerly BS6853, and now incorporated in the European railway standard for fire safety EN45545, include some of the most demanding requirements in the world for composite materials in terms of flammability, smoke and toxic fume emissions.
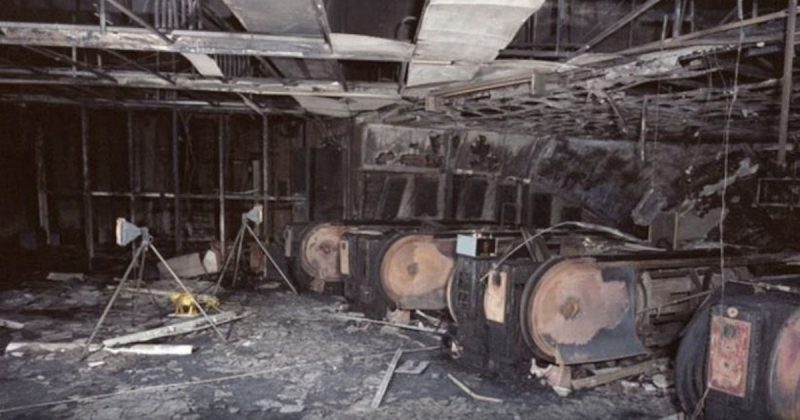
Above: The aftermath of the King’s Cross fire, 1987 [credit: London Fire Brigade]
Following the disaster, Permali’s material scientists worked closely with the technical authorities of London Underground to develop a unique glass reinforced epoxy laminate, Permaglass MER35, that complied fully with the new RSE/STD/014 for fire and arc protection. Since 1990, when Permaglass MER35 and Permaglass MER20 were developed, approved and entered service, they have been used extensively on all new and refurbished rolling stock operating on London Underground, and are used frequently on other third rail networks throughout the world.
This programme of development work, with contributions from industry experts, contributed greatly to Permali’s credibility as a world leading technical authority on the performance and behaviour of fibre reinforced composites when burning.
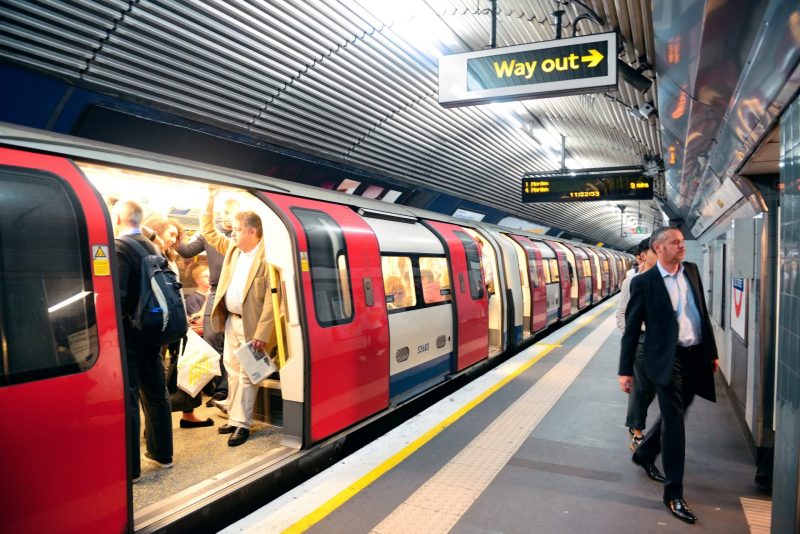
Above: London Underground today
Arc Protection
Modern trains collecting 750 V DC of electricity from a third rail require insulating materials that offer the best possible protection from electrical arcing that occurs at the current collection point. The potential damage and destruction that can be caused by electrical arcing to critical components on the under carriage of modern rolling stock can be catastrophic. Permaglass MER35 has been developed to quench the arcing and limit the electrical tracking that can follow, offering the best protection possible for passengers and expensive equipment.
Fire, Smoke & Toxic Fume Emission Protection
Permaglass MER35 incorporates a high-performance fire retardancy system into its epoxy resin. The complex nature of these fire-resistant additives requires a combined construction of woven and non-woven glass reinforcements to offer outstanding protection in a fire situation – self extinguishing with low smoke and toxic fume emissions when burning.
High Strength
Extreme track forces transmitted through the bogie into current collection gear can put high stress loadings on critical safety components. Permaglass MER35 is designed to offer high strength and excellent resistance to fatigue to ensure train operators have components made from materials with a strong track record of reliable performance. Permali’s expertise in design supports our customers in ensuring all load carrying features are optimised through design to ensure fitness for purpose.
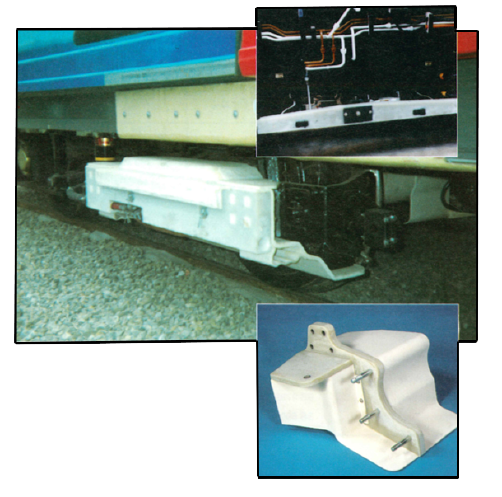
Above: Permali’s MER35
Precision Components
Permali compliments it’s material manufacturing capabilities with precision machining, assembly, and inspection capabilities – ensuring your shoebeam and arc barrier components are not only compliant with current standards but manufactured and assembled to exacting standards. We operate on a 10,500m2 site in Gloucester, UK.
Put Permali to the test, email us at sales@permali.co.uk