What is a Pre-preg?
A pre-preg is a semi-finished material used in the manufacture of high-performance composite parts. It refers to fibres “pre-impregnated” with a plastic or rubber resin system.
Making composite parts from pre-preg allows for a higher ratio of fibre vs resin when compared to other composite manufacturing methods, resulting in higher mechanical strength. It also allows consistent and repeatable parts to be manufactured and is favoured for demanding applications such as aerospace and motorsport, as well as lightweight composite armour.
How are composite pre-pregs manufactured?
Composite pre-pregs can be manufactured from many types of fibre including glass, carbon and aramid but also natural plant-based fibres such as cotton or flax. The resin can be a range of thermoset, thermoplastic or rubber materials. The choice of fibre and resin allows a wide range of different properties to be achieved in the final part.
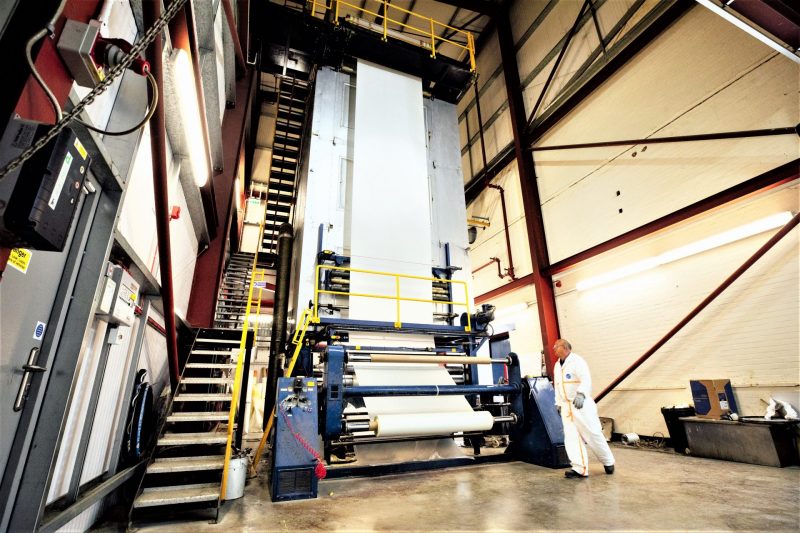
Above: Permali’s Tower Impregnator
As an advanced material solution, Permali typically uses formulations based on epoxy resin for high-strength or electrical insulating applications, and phenolic resin for fire resistance or ballistic properties. In both cases, Permali develops its own proprietary resin blends by adding various additives or fillers to improve properties such as strength or flammability performance. By having full end-to-end control of the materials and manufacturing processes, Permali is able to optimise the performance of the final product. We can make to a maximum width of 1.9m and generally up to 840gsm, however we can be accommodating for bespoke requests. Most commonly we use the fibres; E-glass, S-glass, Aramid and Polyester. It is also possible to use Nylon, Basalt or Cotton in some cases. Our forms are yarn-based fabric, woven roving, tissue and stitched bi-axial.
The impregnation process involves taking rolls of fabric and passing them through a bath of the resin, and then rollers and scrapers that control the resin content. The wet fabric carrying the resin is then passed through an oven to evaporate solvent, and the solvent is then neutralised in the solvent abatement equipment. The resin may also be partially cured in the oven, in a process known as “B Staging”. The B Staging affects how much the resin flows during subsequent manufacturing processes.
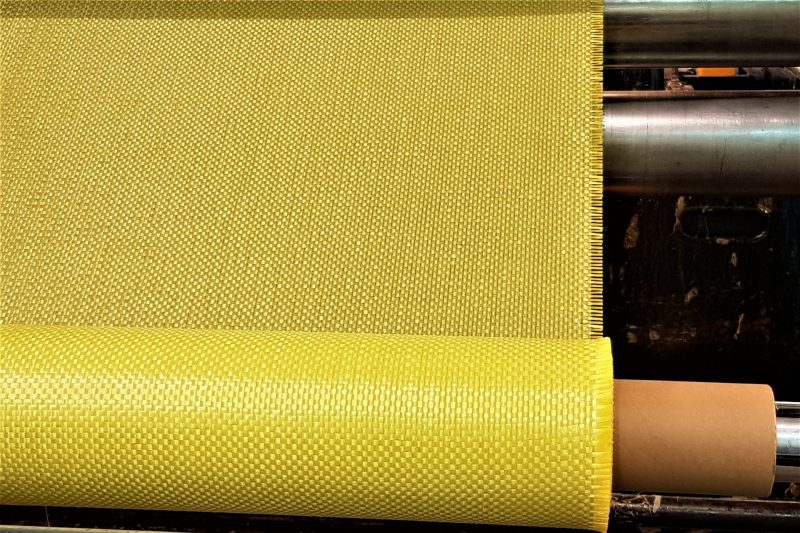
Above: Pre-preg
Once the composite pre-preg is manufactured, the next step is to consolidate and cure one or more layers under heat and pressure. There are several ways of applying heat and pressure, including laminating in a heated platen press, or in an autoclave. Autoclaves operate at lower pressures than platen presses, and so require more resin flow during the cure cycle. For this reason, pre-pregs for autoclave manufacture have low levels of B Stage and are “tacky”. Pre-pregs for platen pressing under higher pressures generally have higher levels of B Stage and less flow, which gives the advantage of a longer shelf-life and less demanding storage conditions.
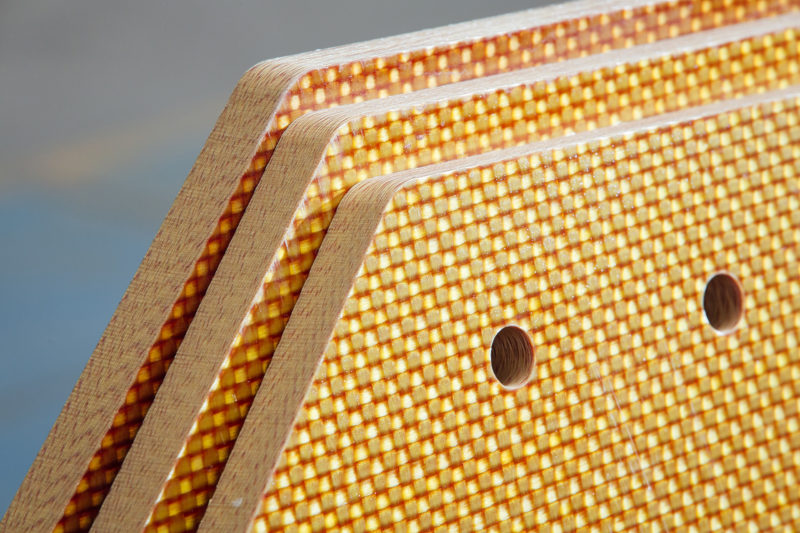
Above: Permali’s pre-preg pressed to composite
Applications of Pre-pregs
Pre-pregs are an important component in the manufacture of high-performance composite parts. They offer maximum strength, high quality and consistent performance and are the material of choice for applications such as aircraft interiors and racing car chassis. Use in other critical parts such as aircraft primary structures, automotive bodywork and train structures is expanding rapidly, and the increasing availability of natural fibres and bio-resins allow “green” composite parts to be manufactured.
Put Permali to the test, email sales@permali.co.uk